A Year In, Sanofi's Journey With Plai AI Is Aiding Quality Decisions
A conversation with Miguelina Matthews, Ph.D., Sanofi
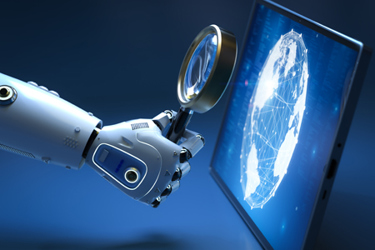
Sanofi has been especially vocal about its artificial intelligence intentions. The company has said it wants to pioneer AI and to become the “first pharma company powered by artificial intelligence at scale.”
When more than 100,000 people work for you in more than 100 countries, any universal technology rollout demands an intelligent strategy. Sanofi appears to be making good on its plans and has charted some real-world experience with meaningful technology.
Ahead of the 2024 International Society for Pharmaceutical Engineering (ISPE) Annual Meeting & Expo, Sanofi’s head of external liaison, Miguelina Matthews, is preparing to talk about the company’s experience with one tool in particular, a platform designed by Aily Labs, which it implemented in June 2023. The tool, which is called “plai,” uses AI to synthesize company-wide data and help teams make decisions.
Matthews agreed to answer a few of our questions about the technology and preview her presentation. Here’s what she told us.
You focus on use cases, which we could summarize as data centralization for deviation and complaint monitoring. Can you offer a quick overview of the initiative?
Matthews: Per our CEO, Sanofi has gone “all in on AI.” We have adopted the use of digital and AI tools across the company. The use case we will describe, known internally as “plai,” is a mobile and web app with real-time, reactive data dashboards, giving us a 360-degree view across all our activities. The tool is used by multiple functions, including finance, manufacturing and supply, and quality. The presentation will focus on how the tool has benefited quality activities, allowing for risk-based decisions based on the insights from the tool, such as trends and potential root causes.
Investing in tools is one thing; using them properly is another thing entirely. Talk about the issues that come up when implementing new technology among teams and the people in them. How did you solve those issues?
Matthews: With any new technology, there may be some apprehension. Communication is key to ensure the tool is understood and used appropriately. In addition, it’s understood that these types of tools work best when the data is reliable and accurate. Several communication and training sessions have been held. We have had communications from senior leaders, including our chief quality officer, sharing the benefits and limitations of the tool. Internal subject matter experts have also reinforced use of the tool during routine site visits. Communication is ongoing as the tool evolves and as we adopt and implement new ones. There are ongoing efforts to ensure that the data is accurate and reliable, and that adoption of the tool is enjoyable.
Does anyone remember when they got their first smartphone or when they used a new app? It takes time to get familiar with the technology. You have to play with it. In the case of plai, we are “playing with plai” to increase fluency. We have deployed periodic quizzes with a gaming and competitive approach. This has also helped us embrace the tool.
Can you give some examples of how a "360-degree" operational view has helped teams make better decisions?
Matthews: With real-time, user-friendly data visualization from the tool, we can reinforce our decision-making 24/7, not just during quarterly/annual reviews. At the global level, the tool has allowed the corporate GxP quality audit function to focus on areas of potential risk and to adjust the audit schedule accordingly. At the entity level, the tool has allowed investigators probing deviations and complaints to consider root causes they may not have considered otherwise. By having access to information from different business units across all of the company, we can use this data to better inform our work and ensure that we work in lockstep.
Was the tool available off-the-shelf? How much custom development did you do?
Matthews: This tool is available in the market and has not been designed specifically for Sanofi. Nevertheless, Sanofi requested several customizations to fit with the business. In addition, for each new use case, the Sanofi team is working closely with developers from an external company to define and design the model.
Can you quantify the time-saving benefit of these tools versus the older, more manual way of doing things? In other words, what's the value case for companies to implement such tools on their own?
Matthews: At the global level, the tool has allowed the corporate GxP quality audit function to focus on areas/sites of potential risk, and to adjust the audit schedule and agenda accordingly. This is expected to save time and cost on travel for audits.
At the entity or site level, in managing deviations and handling complaints, while exact time savings aren't quantified yet, teams anticipate significant efficiency improvements. The tool’s predictive capabilities enhance deviation complaint management, promising substantial operational benefits and cost savings. We have deployed another tool based on generative AI to assist with writing product quality reviews. That tool has reduced the time of PQR writing approximately eight-fold. So, we are confident that our plai tool will also result in time-savings.
Based on the successes and challenges of the tool, describe your outlook for the future. Are you eager to integrate more AI/ML into processes?
Matthews: Yes. This specific tool is increasingly adopted in routine operations, and new digital and AI use cases are continuously being proposed.
The objective remains consistent: data democratization and improving performance by focusing on actionable insights. Specifically for quality, a use case on site risk exposure is currently under definition. Additionally, we are assessing the connections between three modules (quality assurance, manufacturing, and supply) to ease navigation and to emphasize correlations. This integration aims to further enhance the efficiency and effectiveness of our processes.
About The Expert:
Miguelina Matthews, Ph.D., an active member of ISPE, has over 20 years of experience in the pharmaceutical industry, working with a broad range of products, including vaccines, small molecules, consumer healthcare products, and medical devices. She earned a Ph.D. in microbial pathogenesis from Yale University.