A Snapshot Of What Pfizer's Doing With Teleoperated Robots
A conversation with Jean-Maxime Guay, Pfizer Canada 
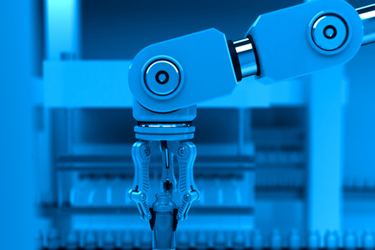
Remotely operated or “teleoperated” robots give flexibility to operators working in highly segregated environments where automation or isolators are inadequate.
Pfizer is testing applications and sees opportunity especially when handling highly potent APIs and for fill/finish operations, among other functions.
In January, Pfizer Senior Manager of Manufacturing Intelligence Jean-Maxime Guay spoke about their evaluations with SRI International on the XRGo system at the International Society for Pharmaceutical Engineering’s 2025 ISPE Facilities of the Future conference.
We asked him to share some of the highlights. Here’s what he told us.
Let's start with an overview. Can you briefly describe the technology and offer a use case or two?
Teleoperated robotics involves the real-time remote operation and control of a robot by a human. It essentially offers the best of both worlds by combining the precision, cleanliness, and safety of robots with human intelligence and decision-making capabilities.
This technology has long been utilized in aerospace, medical, and security (bomb disposal) applications, but its use in industrial manufacturing has been limited. The primary reason is that automation and robotics are adequate for most operations, and the investment in teleoperation is often not justified when safe manual interventions are feasible. In industries requiring cleanrooms, such as pharmaceuticals, food, or semiconductors, telerobotics allows for complete segregation between operators and processes. This remains true even during non-routine corrective interventions, thereby minimizing the risk of contamination.
The technology under evaluation at Pfizer includes hardware components such as stereo cameras, a virtual reality headset, input devices and controllers, communication systems, and a robotic arm. This technology has the potential to enable remote robotic manipulation without direct visual contact by the user. We see a lot of potential from this technology to enable gloveless isolator operations in aseptic fill/finish, where all interventions could be either automated or teleoperated. For rare or complex interventions, full automation may not be cost-effective to research.
Can you talk about specific environmental and technical challenges when installing, validating, and using a remotely operated robot?
Installing any robotic system involves several considerations from integration, validation, and safety perspectives. Additionally, for teleoperated robotics, it is necessary to demonstrate that the system can perform tasks with sufficient precision, efficiency, and consistency between runs.
If the robot is installed in an isolator or restricted access barrier system (RABS) with unidirectional airflow systems, testing the system's ability to maintain sterile conditions while operating the robot is crucial.
An additional challenge is that remotely operated robot motions are less predictable compared to automation, which may result in potential disruptions to laminar flow or compromised integrity of the physical barrier. Virtual barriers are employed in configuring robotic applications to mitigate these risks.
Any suggestions for companies just starting to use telemanipulated robots?
We are in the early stages, but one of our initial observations is that not all processes can be automated, although most can. Therefore, it is important to properly scope the potential application and break down a process into steps for feasibility assessment.
We found that, in many cases, over 90% of a task is highly repeatable, while the value of teleoperation lies in the remaining portion. This should be considered when evaluating the complexity and potential efficiency of telerobotics for a specific use case. Additionally, while some use cases can be addressed as stand-alone applications, teleoperation is more likely to succeed as an enhancement to an overall robotic strategy.
Do they have any utility in day-to-day operations? Are they just for interventions?
It’s a mix. The development of highly potent active pharmaceutical ingredients (HPAPIs) such as antibody drug conjugates (ADCs) is growing rapidly. This growth necessitates more specialized containment areas, equipment, and procedures to prevent exposure of personnel and the environment.
The adoption of new technologies to handle HPAPIs safely and efficiently is increasing, and telerobotics may soon become a regular part of manufacturing or research facility operations.
Beyond fill/finish, what other critical areas within biopharmaceutical manufacturing do you see telemanipulation offering significant benefit?
Certain activities both upstream and downstream of the fill/finish process may benefit from telemanipulation. Material dispensing is one such activity, where operators handle pure compounds, including potentially cytotoxic substances, and any breach in their gowning and protective equipment could have serious consequences.
Quality control (QC) operations represent another area where a flexible workstation capable of conducting various assays with minimal manual intervention could leverage a teleoperated robotic cell. Additionally, the use of telerobotics for training purposes is an interesting prospect. Similar to a surgeon becoming proficient with a specific orthopedic procedure, an analyst or operator could train for particular tasks in a virtual environment to enhance their skill and efficiency.
Incorporating additional features such as haptic feedback would significantly enhance the user experience, contributing to a more immersive environment. Furthermore, after a task has been performed multiple times, it is possible to utilize machine learning software solutions to automate the task in an optimized manner. For quicker motion training, some solutions provide a simple replay function, allowing a task or intervention to be performed once under human control and then executed automatically as needed.
About The Expert:
Jean-Maxime Guay is a senior manager of manufacturing intelligence at Pfizer where he oversees the company’s advanced robotics program.